Application of cast aluminum alloy
- 2021-09-14-
Among the cast alloys, cast aluminum alloys are the most widely used, and other alloys cannot compare. The types of cast aluminum alloys are as follows: Due to the different compositions of aluminum alloys, the physical and chemical properties of the alloys are different, and the crystallization process is also different. Therefore, according to the characteristics of aluminum alloy, aluminum castings should reasonably choose casting methods to prevent or reduce casting defects within the allowable range and optimize casting. 1. The casting technology performance of aluminum alloy is related. The casting process performance of aluminum alloy is generally understood as a more prominent combination of performance in the charging type, product forming and cooling process. Fluidity, shrinkage, air tightness, casting stress, air absorption. These characteristics of die-casting aluminum casting aluminum alloy depend on the alloy composition, but also related to casting factors, alloy heating temperature, mold complexity, exit system, exit shape, etc. 1) Fluidity; fluidity refers to the ability of the alloy liquid to fill the mold. The fluidity determines whether the alloy can cast complex castings. Eutectic alloys have better fluidity in aluminum alloys. There are many factors affecting the fluidity of automotive aluminum castings, mainly including composition, temperature and solid particles of contaminants such as metal oxides and metal compounds in the alloy liquid. However, the fundamental external factors are injection temperature and injection pressure (commonly known as injection head). In actual production, when the alloy has been determined, in addition to strengthening the smelting process (refining and slag removal), it is also necessary to improve the mold processability (sand mold air permeability, metal mold exhaust and temperature), without affecting the casting quality, and improve The pouring temperature ensures the fluidity of the alloy.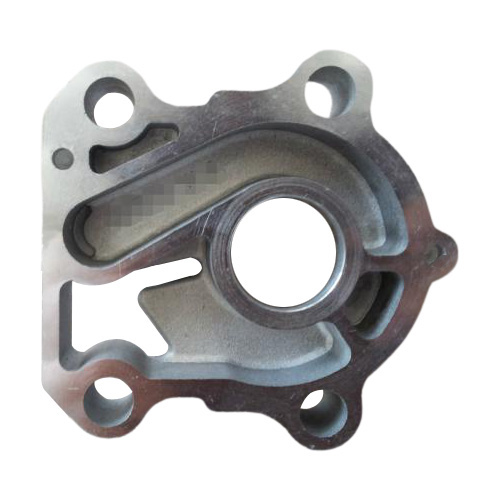